Cantech Letter interviews Suncor
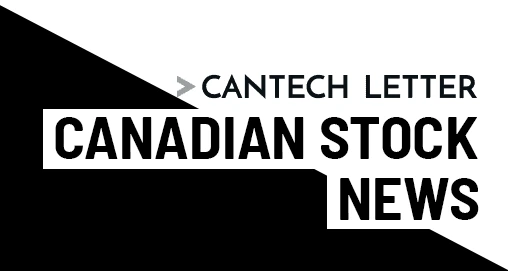
On the morning of April 28th, 2008, Robert Colson, a heavy equipment operator with Syncrude, was working near the company’s Aurora tailings pond, a body of water used to process oil sands waste products that is located about 75 km north of Fort McMurray.
Between 8:45 and 9 a.m, according to transcripts, Colson saw some “lumps” in the pond. “I walked to the edge of the dike … and I noticed it looked like lumps,” he said. “It just looked odd to me, you know what mean? But I wasn’t really close enough to it to tell what it was, so I was in the area for a few more minutes and I noticed a few birds come in and land at that time, and that’s when I realized what was going on.”
On Friday, June 25, 2010, in a packed courtroom in St. Albert, Alberta, Judge Ken Tjosvold found Syncrude legally responsible for the death of 1606 ducks. On October 22nd, he approved joint sentencing submission from the company and Crown lawyers that Syncrude should pay $3 million dollars in penalties. Tailings ponds had attracted attention from the international media before, but this ruling made them a focal point, and heightened oils sands protests in general. What may be a source of worry to oil sands producers is a growing corporate boycott now includes the likes of Levi- Strauss, Walgreens, The Gap and Timberland.
In response the to the growing international criticism, The Energy Resources Conservation Board (ERCB) a self -described “independent, quasi-judicial agency of the Government of Alberta.” launched Directive 074: Tailings Performance Criteria and Requirements for Oil Sands Mining Schemes” requiring operators to prepare tailings plans and report on tailings ponds annually.
This past summer, the ECRB conditionally approved a plan by Suncor Energy Inc. for improving fluid tailings management. Suncor has been working on a plan called TRO (Tailings Reductions Operations), a technology the company expects to invest more than a billion dollars into. Cantech Letter talks with Suncor spokesman Dany Laferriere about the company’s progress in this area.
1. Dany, Suncor just unveiled the first reclaimed tailings pond in the country north of Fort McMurray. Can you tell us about the technology used to do this?
DL: The recent milestone you mentioned is the surface reclamation of Suncor’s first storage pond for oil sands tailings when commercial production began in 1967. Known as Pond 1, Suncor has renamed the area Wapisiw Lookout to pay tribute to the history of the region. Tailings technologies have advanced significantly since Suncor built Pond 1 but the Construction of Pond 1 pre-dated the availability of modern tailings management technologies and, as such, these technologies were not used to achieve the milestone. This Pond 1 reclamation process started with infilling the pond with 30 million tonnes of reclaimed tailings sand. Drainage systems and swales were then developed to manage water runoff from the pond. As these activities were completed, landscaping activities began, which involved placing 1.2 million cubic meters of topsoil over the surface, to a depth of 50 centimetres.
2. How long has Suncor been working on this technology, and how much money have you put into it?
DL: Suncor has been researching, developing and testing the TROTM technology since 2003. Earlier this summer, Suncor received approval to implement it across its existing operations. The company expects to invest more than $1 billion to implement the TRO technology over the next two years, potentially reducing tailings reclamation time by decades and speeding the return of oil sands mining sites to natural habitat.
3. How long before tailings ponds are a thing of the past?
DL: What TRO does is reduce the need to build more tailings ponds, as the MFT is consumed as it is generated; it also accelerates the reclamation time of mined areas and enables us to reduce the company’s overall tailings inventory. There is still a need for ponds as tailings need to settle for a few years before they can be processed and dried, but the process will help minimize the number of ponds that we will need. We expect that in 20 years, if you flew over our site, you’d see significantly less water than you do today as well as more reclaimed areas and evidence of ongoing reclamation. Suncor learned a great deal in completing the surface reclamation of Wapisiw Lookout. The company will use this knowledge along with new and developing innovations to manage our tailings and speed up the reclamation of other existing tailings ponds.
4. The use of water is a big issue in the oil sands. Are you taking steps to reduce water usage?
DL: A long-winded answer but that’s an important question … Water is an essential part of Suncor’s operations. We also recognize water is a precious resource and we are committed to using it wisely by becoming more efficient, investing in technology and collaborating with stakeholders on regional solutions. We use water in the bitumen extraction process, as cooling and process water during upgrading, and to generate steam at our in situ operations. Our refineries also require water for heating and cooling. Our commitment to sustainable development means balancing our company’s water requirements with the need to maintain a clean, safe and plentiful supply of this important natural resource. Although our water withdrawal from the Athabasca is currently less than 0.3. per cent of the river’s flow, we’re making concerted efforts to use less water. At our oil sands mining operations, we’ve reduced total withdrawal from the Athabasca River by more than 27.5% since 2004 — including an 11% reduction in 2009 alone. Our water withdrawal is the lowest since 1998, even though bitumen production more than doubled during that time. We focus on reusing and recycling water in our operations whenever possible as an alternative to fresh water. We are using municipal grey water instead of fresh water at our Edmonton refining facilities. Under normal conditions, about 75 per cent of the water Suncor uses at its oil sands mining operations is recycled. The recycling ratio at our in situ facility is at or above 90 per cent. And we
continue to look for ways to improve this performance. Suncor’s internal water task force oversees day-to-day water management efforts at our oil sands facility, including finding ways to increase recycling and improve internal monitoring and reporting of water use. Water has been identified in our Environmental Excellence strategy as a focus area for conservation efforts. In fact, last summer, we committed to further reducing our water intake by 12% by 2015, compared to 2007 levels. 2009 marked the first full year of Suncor’s 10-year oil sands water management plan aimed at making the company the lowest net water intensity user in the oil sands mining business. We have more than $500 million in capital to implement this plan.

Nick Waddell
Founder of Cantech Letter
Cantech Letter founder and editor Nick Waddell has lived in five Canadian provinces and is proud of his country's often overlooked contributions to the world of science and technology. Waddell takes a regular shift on the Canadian media circuit, making appearances on CTV, CBC and BNN, and contributing to publications such as Canadian Business and Business Insider.